Texture Division
TANAZAWA recognized around the world
In the 1960s, when etching grains were monotonous and flat, we developed 3D-etching, which was revolutionary at the time. With this, we were able to create a natural grain that reproduces the delicate characteristics of genuine leather. Since then, we keep brushing up our technical skills searching for even better texture.
We keep trying to perform specific textures such as; adding functions to molds, or; texturing molds for vacuum/foaming that replaces electroforming with high design quality and lightweight as well.
We, growing together with Japan’s mold industry, in today’s increasingly globalized world, continue to support customer’s needs with our technological capabilities and deliver safe and stable Japan Quality to the world.
What is SHIBO process?
The wrinkles seen on the leather surface are called “shibo(シボ)”
Before the Kamakura period, the unevenness of Eboshi (hat) was called “shibo(しぼ).”
In the leather processing and textile industries, wrinkles were also called shibo(皺). Our founder took a hint from this and named the process of adding patterns to the surface of the mold “shibo-tsuke(しぼ付け) (applying texture/grain).”
After 1945, Japan’s plastics industry developed rapidly. We were the first to pay attention to that. Texturing, which increases product value through decorative effects, has become essential in plastic molding.
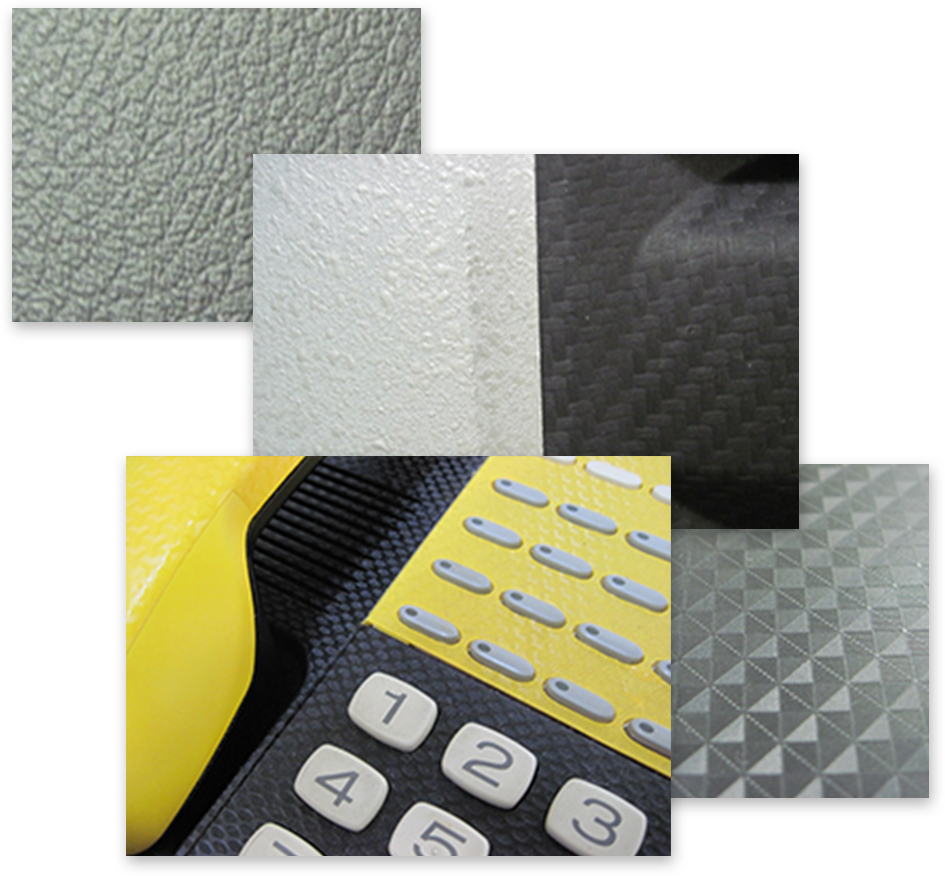
Worried with any issues on plastic parts?
Example1
Direction of improvement for molding defects
When sandblasting or polishing do not help…
Example2
High added value
Why not give it a try with SHIBO?
- Has a kind of nice to touch…
- Well drains…
- Less water droplets…
- Our Solutions
- Adding something with SHIBO may work to resolve.
Example3
For making presentations…
In such scene before mass-production
- Our Solutions
-
- Presentations internally → Banatone, Real-tech
- Photo shooting, Video shooting → Banatone, Real-tech
- Identifying possible problem before production → Real-tech 2
Example4
For cost-saving
If you wish to;
- reduce molding material…
- reduce paints…
- reduce frequency of cleaning the molds…
- confirm beforehand…
- minimize retouching…
- Our Solutions
- What is the obstacles to cost reduction for you? Please feel free to let us know. Our technology might be a key to solve the problem.
- Texturing by TANAZAWA HAKKOSHA
- Leather / Line / Grid / Diamond cut / Dimples / Geometric / Fabric / Stitches / Weaving / Lace / Wood / Stone / Stipple / Painting / Sand matt / Hairline / Super low gloss / Laser-feel and more….
Should you have any concerns about design or quality control,
please contact TANAZAWA HAKKOSHA, Japan’s leading texturing company.
Molds / Molds for molding / Rollers
Ready to use our original lineup (TH / Leo / KODAMA / Haptic / Hydrophilic / Water repellent) is available.
Exclusive pattern as you want is also available, by combining various techniques.
- Chemical etching:This is a technology that forms a designed acid-resistant resist membrane on a metal surface and etches and engraves the exposed metal parts with acid, etc. Cost-effective process that is suitable for mass-production using metal molds.
- Sandblasting:Fine particles such as silica sand are blasted onto the surface at high speed using a compressed air. Spray-grained surface can be finished as desired with matte, glossy or half-matte.
- Lasering: CO2/fiber laser melts and sublimate the surface.
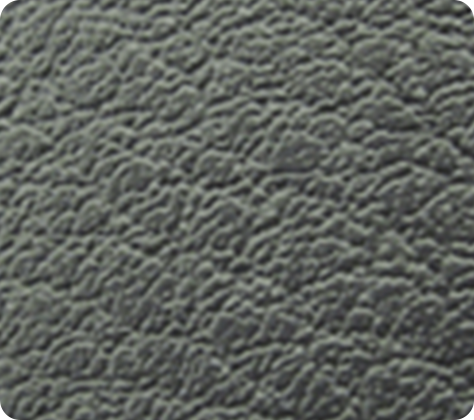
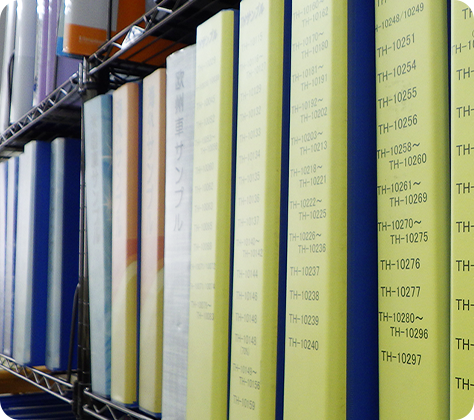
Molded parts / Prototype
Texturing on the product is also available. Not only on a single part for review, for an urgent need or for master model of rapid prototype, there are various ways to use these options:
- BANATONE: 3D pattern is created with the data (No master pattern required)
- Real-tech:Texture pattern is created from a ‘Master pattern’. Suits for creating realistic pattern.
Texturing for small quantity molding is also available, which can be used to verify flow analysis results or check the appearance of weld lines.
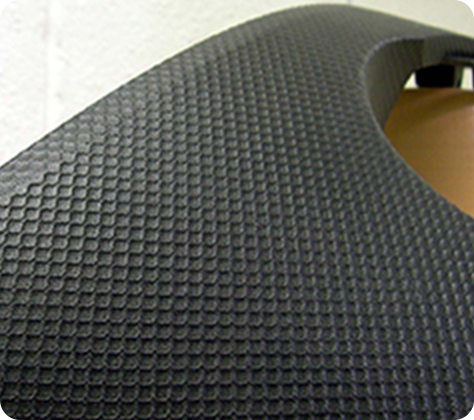
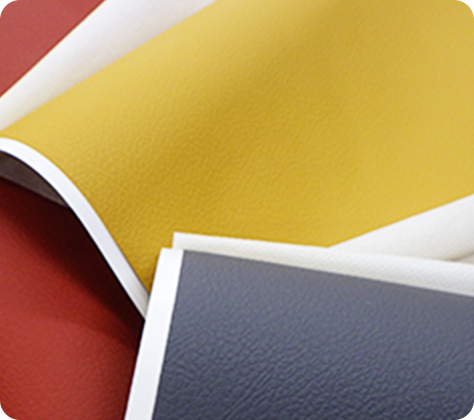
Special processing
Completely new processing method that meets the needs for mold materials that cannot be etched, small-volume production products, and the need for authenticity.
Attracts attention as a new solution to reduce appearance defects such as weld lines.
- Cerashibo:Texture pattern is formed on the mold surface using a special heat-resistant and wear-resistant material. No need to consider etching properties of mold material. Reproduces the rich expression of Washi (Japanese paper) and the feel of linen weave. For custom specifications and limited edition products. Applicable to 3D- printed molds.
- Cera coat:The special surface shape creates a matte, deep black and no gloss appearance that stands out from sandblasting or spray textures.
- Ceramat:Creates a matte, deep black and no gloss appearance that stands out from sandblasting or spray textures. Effective on surface issues such as ghosting or clouds (ghost marks).
- G coat:Uniforms appearance of molded parts with high mold releasability.Also effective as a countermeasure against issues such as ghosting and cloud (ghost marks), and to reduce retouch of weld lines.
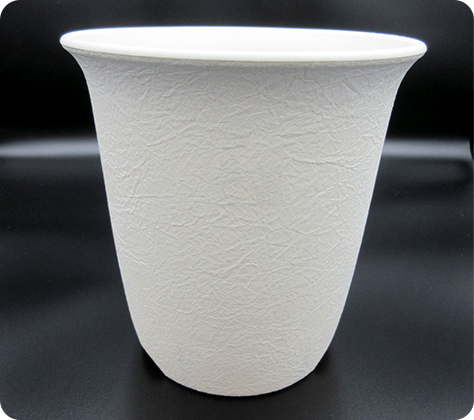
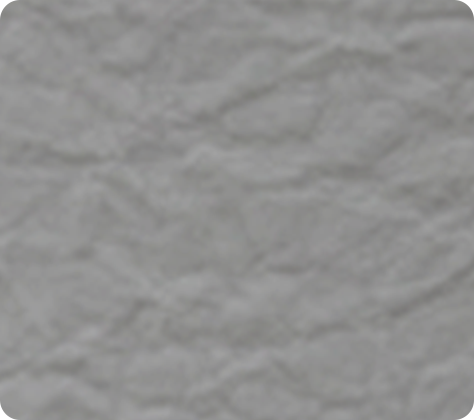